Are you in the market for a new valve, but unsure whether to choose a plug valve or a ball valve? With so many options available, it can be difficult to know which one is right for your specific needs. As a supplier of industrial valves, we often get asked by our customers about the difference between plug valves and ball valves, and which one they should choose for their specific applications. Both valves are commonly used in various industries, but they have their own advantages and disadvantages. In this blog post, we will compare the two types of valves and help you determine which one is the right choice for your needs.
First, let’s take a look at plug valves. A plug valve is a quarter-turn valve that uses a tapered or cylindrical plug to control the flow of fluids or gases through a pipe. Plug valves are designed to provide tight shutoff and are commonly used in applications where a positive shutoff is required. They are also known for their ability to handle high-pressure and high-temperature applications.
On the other hand, ball valves are also quarter-turn valves that use a ball-shaped disk to control the flow of fluids or gases through a pipe. Ball valves are designed for quick and easy shutoff, and they are commonly used in applications where frequent operation is required. They are also known for their ability to handle high-pressure and high-temperature applications.
So, which one should you choose? It ultimately depends on your specific application and requirements. Plug valves are a good choice for applications that require tight shutoff and can handle high-pressure and high-temperature environments. Ball valves are a good choice for applications that require quick and easy shutoff and frequent operation.
When it comes to cost, plug valves are generally more expensive than ball valves. This is because plug valves are designed to provide tight shutoff and are typically made from higher-quality materials. Ball valves, on the other hand, are less expensive and are commonly made from materials such as stainless steel or brass.
Another factor to consider is the maintenance required for each valve. Plug valves require regular maintenance to ensure they continue to provide tight shutoff, while ball valves require less maintenance due to their design. However, if a ball valve fails, it will typically require the replacement of the entire valve, whereas a plug valve can often be repaired.
In terms of flow control, both plug valves and ball valves provide excellent control over the flow of fluids or gases. However, plug valves are generally better suited for applications that require precise control over the flow rate, as the tapered or cylindrical plug can be adjusted to provide precise flow control.
In summary, the choice between plug valves and ball valves depends on your specific application and requirements. Plug valves are a good choice for applications that require tight shutoff and can handle high-pressure and high-temperature environments. Ball valves are a good choice for applications that require quick and easy shutoff and frequent operation. Cost and maintenance requirements should also be taken into consideration when making your decision.
What are the different types of plug valves?
There are several types of plug valves, each with its own specific design and features. Here are some of the most common types:
- Lubricated Plug Valve: This type of valve has a cylindrical or tapered plug that is lubricated to ensure smooth operation. It is commonly used in applications where high-viscosity fluids or abrasive particles are present.
- Non-Lubricated Plug Valve: In this type of valve, the plug is not lubricated and relies on a tight fit between the plug and the body to provide a seal. It is commonly used in applications where cleanliness is important.
- Sleeved Plug Valve: This valve has a sleeve or liner that covers the plug, providing a tight seal and protecting the plug from wear and corrosion. It is commonly used in applications where abrasive or corrosive fluids are present.
- Eccentric Plug Valve: In this type of valve, the plug is offset from the centerline of the valve body, which allows for a wider flow path and reduces turbulence. It is commonly used in applications where low-pressure drop and high flow capacity are required.
- Three-way Plug Valve: This valve has three ports, which can be used to switch the flow of the fluid in different directions. It is commonly used in applications where the mixing or diverting of fluids is required.
- Self-Locking Plug Valve: This valve has a plug that is designed to lock in place when it is fully opened or closed, providing additional safety and security. It is commonly used in applications where safety is a concern.
These are some of the most common types of plug valves. The selection of the right type of valve depends on the specific application and the requirements of the system.
What are the different types of ball valves?
There are several types of ball valves, each with its own specific design and features. Here are some of the most common types:
- Floating Ball Valve: In this type of valve, the ball is not fixed in place and is allowed to float in the fluid. It is held in place by two seals, which provide a tight seal when the valve is closed.
- Trunnion Ball Valve: This type of valve has a fixed ball, which is supported by trunnions or shafts. It is suitable for high-pressure and large-diameter applications.
- Three-way Ball Valve: This valve has three ports, which can be used to switch the flow of the fluid in different directions. It is commonly used in applications where the mixing or diverting of fluids is required.
- V-Port Ball Valve: This valve has a V-shaped ball, which allows for more precise control of the flow of the fluid. It is commonly used in applications where high accuracy and control are required.
- Top Entry Ball Valve: In this type of valve, the ball can be accessed and serviced from the top of the valve. It is suitable for applications where regular maintenance and cleaning are required.
- Fully Welded Ball Valve: This valve has a fully welded body, which provides a high level of strength and durability. It is commonly used in applications where the valve is subjected to high pressures and temperatures.
These are some of the most common types of ball valves. The selection of the right type of valve depends on the specific application and the requirements of the system.
Now, let’s take a closer look at the two types of valves to help you determine which one is right for your needs.
Plug Valves
A plug valve is a quarter-turn rotational motion valve that uses a tapered or cylindrical plug to stop, start, or regulate flow. The plug has a hole or port that allows fluid to flow through it when it is in the open position. When the valve is closed, the plug is rotated to seal the flow path, preventing fluid from passing through the valve. Plug valves are typically used in applications where low maintenance and tight shutoff are required, such as in the oil and gas industry.
Plug valves can be divided into two categories: lubricated and non-lubricated. Lubricated plug valves have a cavity in the plug that is filled with lubricant to reduce friction and wear between the plug and valve body. Non-lubricated plug valves do not have this cavity and rely on the materials used in the valve construction to reduce friction.

Ball Valves
A ball valve is another quarter-turn rotational motion valve that uses a ball with a hole through the center to regulate flow. When the valve is open, the ball is rotated so that the hole is in line with the flow path, allowing fluid to pass through the valve. When the valve is closed, the ball is rotated 90 degrees so that the hole is perpendicular to the flow path, blocking the flow of fluid. Ball valves are commonly used in applications where fast action, tight shutoff, and low maintenance are required.
Ball valves can be divided into two categories: floating ball valves and trunnion ball valves. Floating ball valves use a floating ball that is not held in place by the valve body, allowing it to move slightly to create a seal with the valve seats. Trunnion ball valves, on the other hand, use a fixed ball that is held in place by a shaft or trunnion and rely on pressure from the fluid to create a seal.
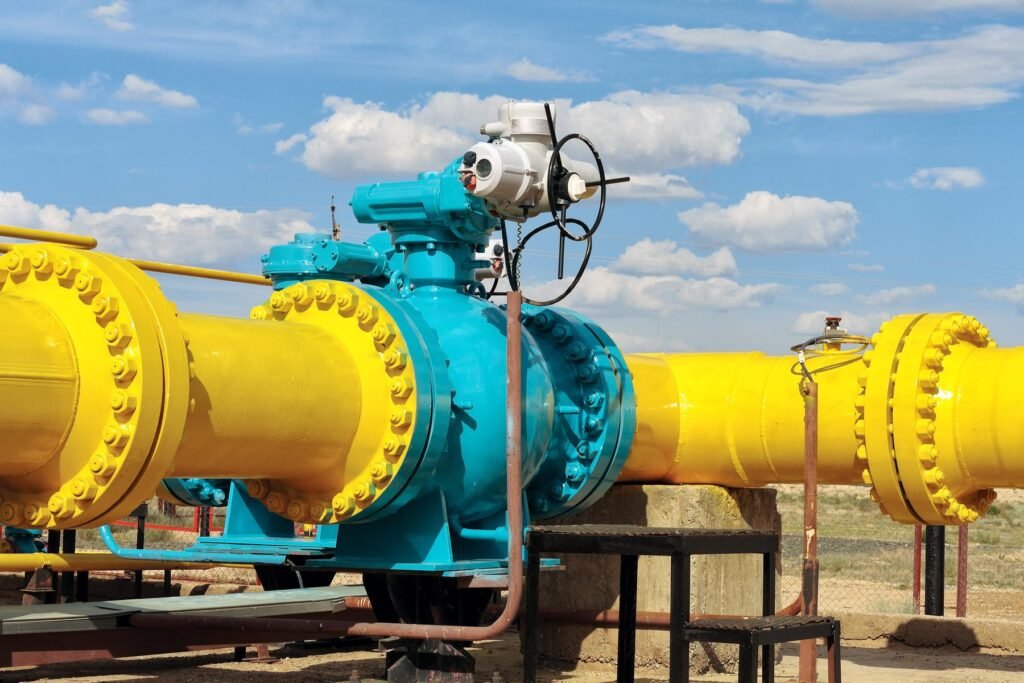
Plug Valves vs. Ball Valves
Now that we have a better understanding of how plug valves and ball valves work, let’s compare the two types of valves to help you determine which one is right for your needs.
Flow Control
Both plug valves and ball valves are capable of regulating flow, but they do so in different ways. Plug valves use a tapered or cylindrical plug to regulate flow, while ball valves use a ball with a hole through the center. Plug valves are better suited for applications that require fine-tuning of flow control, while ball valves are better suited for applications that require quick, on/off flow control.
Pressure and Temperature
The second factor to consider is the pressure and temperature requirements of the application. Plug valves are generally better suited for high-pressure and high-temperature applications, as the cylindrical or conical plug provides a more secure seal than the spherical ball of a ball valve. Ball valves are better suited for low-pressure and low-temperature applications, as the spherical ball provides less resistance to flow than the cylindrical or conical plug of a plug valve.
Maintenance
The third factor to consider is the maintenance requirements of the valve. Plug valves are generally easier to maintain than ball valves, as they have fewer moving parts and are easier to disassemble and inspect. Ball valves, on the other hand, are more complex and may require more frequent maintenance to ensure proper operation.
Cost
The final factor to consider is the cost of the valve. Plug valves are generally more expensive than ball valves, due to their more complex design and higher manufacturing costs. However, the higher cost may be justified in applications that require more precise flow control, higher pressure and temperature ratings, or lower maintenance requirements.
The Benefits of Ball Valves
Ball valves are typically a better choice than plug valves in certain applications due to their design and functionality. They are often used in applications that require a tight shut-off, as their design makes them less likely to leak than plug valves. The ball valve is a quarter-turn valve that uses a hollow, perforated and pivoting ball to control flow through it. When the valve handle is turned, the ball rotates, allowing for precise control of flow.
Ball valves are also less likely to get clogged than plug valves, as they have a large, clear opening that allows for easy cleaning and maintenance. This makes them a great choice for applications where debris or sediment may be present, such as in water treatment plants or oil and gas pipelines.
Another advantage of ball valves is their versatility. They can be used in a wide range of applications, including high-temperature and high-pressure applications. They are also available in a range of sizes, from small quarter-inch valves to large valves that are several feet in diameter.
The Benefits of Plug Valves
While ball valves have their advantages, plug valves are the better choice in certain applications. Plug valves have a tapered or cylindrical plug that rotates within the valve body to control the flow of fluids through the valve. They are often used in applications where a high degree of flow control is required.
One advantage of plug valves is their ability to handle high-pressure applications. They can handle pressures of up to 15,000 PSI, making them a great choice for applications in the oil and gas industry. They are also able to handle high-temperature applications, making them a great choice for applications in the chemical industry.
Another advantage of plug valves is their ability to handle viscous fluids. Their design allows for a large opening, which makes them less likely to get clogged by viscous fluids. This makes them a great choice for applications where high-viscosity fluids are present, such as in the food and beverage industry.
Which One Should You Choose?
When it comes to choosing between a ball valve and a plug valve, there are several factors to consider. The choice ultimately depends on the specific application and the requirements of the system.
If you need a valve that can handle high-pressure applications or viscous fluids, a plug valve may be the better choice. If you need a valve that can handle a wide range of applications, including high-temperature and high-pressure applications, a ball valve may be the better choice.
Another factor to consider is the cost. Ball valves are typically less expensive than plug valves, making them a great choice for applications where cost is a concern.
Ultimately, the best way to determine which valve is right for your application is to consult with an experienced valve manufacturer or distributor. They can help you determine the best valve for your specific needs.
Conclusion
So, which one should you choose? The answer, as with many things in life, is that it depends. Both plug valves and ball valves have their advantages and disadvantages, and the best choice for your application will depend on your specific needs.
If you require excellent shut-off capabilities, precise flow control, high pressure & temperature ratings, and lower maintenance requirements, then a plug valve may be the best choice for you. On the other hand, if you need quick and easy on/off control and lower pressure and temperature ratings, then a ball valve may be the best choice.
Ultimately, it’s important to consult with an expert to determine which valve is best suited to your specific needs. At DSNY Valve, we have a team of experienced engineers who can help you select the right valve for your application. Contact us today to learn more!