Ball valves are generally considered to have no installation direction. Even if ball valves with arrows are occasionally found on the project site, most of them will be installed in the direction of the fluid, but the reason is unknown. With the diverse needs of customers, progressing engineering technology and equipment, valves that meet different working conditions are also emerging. In fact, some fixed ball valves have installation direction requirements, such as DBB & DIB ball valves. This article will focus on the analysis of sealing structure and directionality of the DBB and DIB Trunnion ball valve.
Seal Mechanism of The Trunnion Ball Valve
As we all know, the ball of a trunnion ball valve has upper and lower shafts, which are fixed in the bearing of the ball. Therefore, the ball does not float but the sealing ring floats. The seal ring is pressed against the ball by the thrust of the spring and the fluid, creating a seal at the upstream (or downstream) end. Usually, the trunnion ball valves are suitable for high-pressure and large-diameter conditions.
Basic principle of the fixed ball valve sealing: Under the action of pre-tightening force and/or medium pressure, the valve seat and the ball are pressed tightly to generate sealing force. The sealing ring produces elastic-plastic deformation to compensate for the relative deformation, the roundness error and surface roughness of the ball, so that the gap on the sealing surface is reduced to less than the molecular diameter of the fluid to ensure that the fluid will not leak.
Seats with Single-Piston Effect and Double-Piston Effect
The ball of the trunnion ball valve is fixed while the seat is floating. The seat is divided into two types with single piston effect which has self-relieving action, abbreviated as SPE, and double piston effect, abbreviated as DPE.
The principle of the single-piston valve seat is a one-way piston effect. The difference between the forces in two directions on the sealing surface will produce forces in different directions. Under the push of this pressure difference, the sealing ring will produce piston movement in the corresponding direction, which is called single-piston effect.
The principle of the double-piston valve seat is similar to that of the single-piston, but in the design of the sealing ring, it is necessary to ensure that no matter the pressure of the downstream pipeline is higher than the valve cavity or lower, the sealing ring can always achieve sealing, so as to avoid the pressure release of the cavity to the downstream and protect the downstream pipeline, which is called double piston effect.
In short, a single-piston seat only can seals in one direction, while a double-piston seat can achieve sealing in both directions.
The Sealing Principle of Single Piston Effect Seat
In some literature, the relevant mathematical calculations for single-piston and double-piston valve seats are relatively cumbersome. This article mainly uses diagrams to explain the sealing principle combined with the force of the valve seat.
In Figure 1~4:
FF is the spring force, and the direction of the arrow indicates the direction of the force;
F△A is the pressure difference generated by the fluid on the valve seat (That is, the product of the area difference between Aa and Ai and the pressure);
FR is the final resultant force on the valve seat, and the direction of the arrow indicates the direction of the force.
In Figure 1, when the fluid flows from right to left, obviously the direction of the resultant force FR=F△A + FF (where △A=Aa- Ai>0) is from right to left, pushing the seat against the ball to achieve a seal.

In Figure 2, when the pressure in the valve cavity increases, a thrust F△A from left to right is generated (where △A=Aa- Ai<0), the force FF of the spring is now from right to left, and the resultant force FR produced is to the right, pushing the valve seat away from the ball to realize the discharge.

The Sealing Principle of Double Piston Effect Seat
In Figure 3, when the fluid flows from right to left, obviously the direction of the resultant force FR=F△A + FF (where △A=Aa- Ai>0) is from right to left, pushing the seat against the ball to achieve a seal.

In Figure 4, when the pressure in the valve cavity increases, a thrust F△A from right to left is generated (where △A=Aa- Ai>0), and the force FF of the spring is now also from right to left. Obviously, the direction of the resultant force FR=F△A + FF is from right to left, pushing the seat against the ball to achieve a seal.

The Difference Between Single Piston Effect and Double Piston Effect
- The pressure discharge of the cavity is different: the double piston effect design is to discharge when the cavity pressure exceeds 1.1~1.33 times of the corresponding value of the pressure level, and discharge to the atmosphere. The single-piston effect design is to automatically discharge to the downstream pipeline as long as the pressure difference between the cavity and the downstream acting on the annulus of the valve seat is greater than the pressure of the loading spring.
- The leakage probability is different: the advantage of the single-piston effect design is that when the pressure of the valve cavity increases, it can be released upstream (or downstream) automatically, and there will be no danger after the high pressure is established in the valve cavity, but the probability of leakage is double of the double piston effect. Because always the upstream side of the valve plays the role of sealing, if it is damaged, the pressure of the valve body will continue to increase, while the downstream seat doesn’t have the sealing function, and the valve will undoubtedly leak.
Double Block and Bleed (DBB) and Double Isolation and Bleed (DIB)
Because the definitions of DBB & DIB valves are relatively brief and similar in the discussion of API 6D, resulting in some misunderstanding about them. Even some engineers are confused with these two definitions, causing certain technical confusion and supply disputes to the manufacturers’ design departments and users. What’s more serious is that the wrong types for certain working conditions might bring major safety accidents. These two structures are currently most used in plug valves, flat gate valves and fixed ball valves. This article only focuses on DBB and DIB fixed ball valves.
The Standard Definition for Double Block and Bleed (DBB) Valve
A single (non-composite joint type) valve with two seat sealing surfaces, when it is closed, can block the medium from the upstream and downstream at the same time, and the medium in the cavity clamped between the seat sealing surfaces has a release channel.
Note: When this type of valve is only subjected to a single-direction medium pressure (upstream or downstream), it does not have a double isolation function.
The Standard Definition for Double Isolation and Bleed (DIB) valve
A single (non-compound type) valve with two seat sealing surfaces, when it is closed, each seat can independently isolate (seal) the medium pressure from both sides (pipeline and valve cavity), and the medium in the cavity clamped between the seat sealing surfaces has a discharge channel.
Note: The valve can be assembled with one or two double-piston seat.
In addition, according to the Appendix B of API 6D, the DIB can be subdivided into two types: one is DIB-1, which with two isolation seats (that is, double-piston valve seats); the other one is DIB-2, which with one isolation seat (double-piston valve seat) and one single-piston valve seat.
Analysis of DBB and DIB Fixed Ball Valves
Two-way sealing fixed ball valve (that is, when the ball valve is closed, it can block the fluid on both sides of the valve at the same time), but this does not mean that the seat is two-way sealing, a two-way ball valve may be composed of two single piston seats, maybe a single piston seat and a double piston seat, or two double piston seats. This means that the two-way sealing of the trunnion ball valve and the two-way sealing of the seat are two different concepts, which must not be confused.
Performance Comparison of DBB and DIB Trunnion Ball Valves
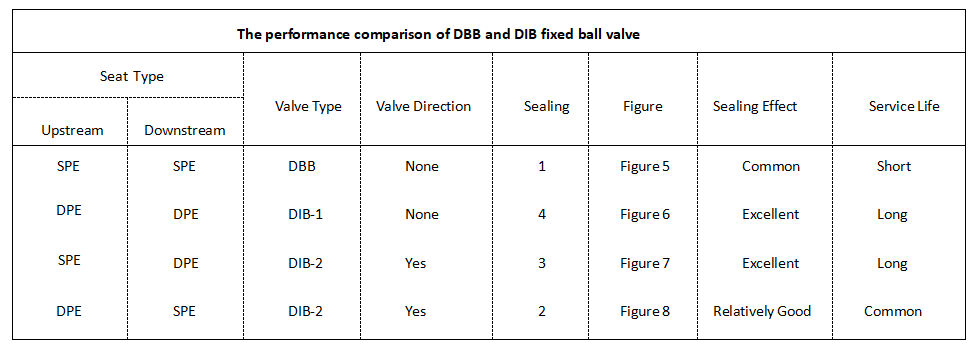
If we use the →| symbol for the SPE piston, and the →|← for the DPE, then the above four types of valve can be marked with Figures 5-8.

In Figure 5, when the fluid flows from left to right, under the action of fluid pressure, the upstream valve seat (SPE) is close to the ball to achieve sealing while the downstream valve seat does not have a sealing effect at this time. And when a large amount of high-pressure gas is generated in the valve cavity, and the generated pressure is greater than the spring force of the downstream valve seat, the downstream seat will be bounced open to realize pressure relief. Contrarily, when the downstream valve seat acts as a seal, the upstream seat will act as an overpressure relief function, which is the origin of the double block and bleed valve.

In Figure 6, when the fluid flows from left to right, the upstream valve seat (DEP) and the downstream valve seat both can play a sealing role. The downstream seat actually plays the role of double insurance in the application. When the upstream seat leaks, the downstream seat remains sealed. Similarly, when the fluid flows from right to left, the downstream valve seat plays a major sealing role, and the upstream valve seat plays a double insurance role. The disadvantage is that when high-pressure gas is generated in the valve cavity, the seats cannot realize pressure relief, which may require a safety relief valve connected to the outside of the valve, so that the rising pressure in the cavity can be released into the atmosphere, but at the same time increase a leakage point. If the gas is toxic or corrosive, it will also cause pollution or life hazard.

In Figure 7, when the fluid flows from left to right, the upstream valve seat can play a sealing role, and the downstream two-way valve seat can also play a double sealing role, so that even if the upstream valve seat is damaged, the downstream valve seat can still maintain the seal. When the internal pressure of the cavity suddenly rises, the pressure release can be realized through the upstream valve seat. It can be said that its sealing performance is similar to that of the two-way valve seats of DIB-1, but it can realize spontaneous pressure relief at the upstream seat end, which combines the advantages of both DBB and DIB-1 valves.

Figure 8 has almost the same function as Figure 7, the only difference is that when the pressure in the valve cavity rises, the downstream valve seat realizes spontaneous pressure relief. Generally from the perspective of technology, it’s more rationality and safety to release the abnormal pressure of the cavity to the upstream. So the former design will be used sometimes, but the latter design is lack actual value and rarely be used in practical applications.
It should be emphasized that generally the upstream valve seat plays the main role of sealing, so the probability of damage is relatively high due to its frequent use. At this time, if the downstream valve seat can also play a sealing role, it will be insurance and can extend the life of the valve. That’s why the service life of DIB-1 and DIB-2 (SPE+DEP) valves is longer than other valves.
Why DIB-2 Fixed Ball Valves Require Installation Direction
(1) Once it is reversed, it will affect the life of the valve
Normally, for the DIB-2 fixed ball valve (SPE+DPE) in Figure 7, when the fluid flows from left to right, the upstream valve seat can play a sealing role. If it fails, the downstream DPE seat can also play a sealing role, so the valve has a high insurance factor and long service life. Once installed in a reversed direction, it will become a DIB-2 valve (DPE+SPE) in Figure 8. At this time, if the upstream valve seat (DPE) fails, the downstream valve seat (SPE) will not be able to seal. Therefore, the insurance factor is not high, and the life is relatively short.
(2) Once it is reversed, it will affect the pressure release of the valve
Normally, for the DIB-2 type valve (SPE+DPE) in Figure 7 , the rising pressure in the valve cavity will be released upstream, which is more consistent with the technical profession. Once it is installed in reverse, it will become Figure 8 and the pressure will be released downstream, which is contrary to the normal technical profession.
Advantages and Disadvantages of These Fixed Ball Valves
Comparison of the advantages and disadvantages of these fixed ball valve
Valve Type | Advantages | Disadvantages |
DBB (SPE+SPE) | One of the upstream and downstream valve seats can realize sealing, and the other one can realize pressure relief. | Only one seat can seal, if this seat fails, the valve will be without a sealing function. |
DIB-1 (DPE+DPE) | Once one of the seats is damaged, the other one can also realize sealing, so the sealing is double guaranteed. | 1. Unable to release pressure spontaneously, need to connect a safety relief valve outside of the ball valve. 2. If the pressure in the valve cavity rises spontaneously and cannot be discharged, it will be dangerous. 3. If connecting an external safety relief valve, there will be an additional leakage point. |
DIB-2 (SPE+DPE) | The unnormal pressure of valve cavity can be released through the upstream seat, at this time, the downstream seat can realize the two-way isolation of the medium. | —— |
DIB-2 (DPE+SPE) | The unnormal pressure of valve cavity can be released through the downstream seat, at this time, the upstream seat can realize the two-way isolation of the medium. | Rarely used in actual situations. |
In summary, it is very important to distinguish these four types of trunnion ball valves. For example, in a pipeline system conveying hazardous medium, mistakenly selected the DBB type instead of the DIB, if the upstream seat fails, the medium is likely to leak into the downstream operation area, causing casualties and equipment damage.
Applications for DBB and DIB Trunnion Ball Valves
The applications comparison of DBB and DIBfixedballvalve
Valve Type | Suitable Applications | Marks |
DBB | 1. Suitable for most ball valve application fields; 2. Suitable for conditions where the medium is not allowed to be discharged out of the valve and will not increase the hazards caused by the leakage of flammable and explosive media such as oil and natural gas; 3. Usually be used in applications with normal temperature and pressure, mild conditions, non-toxic and harmless medium; 4. The applications where need to consider economics on the premise that there are no potential safety hazards. | Usually widely used. Generally, companies regard single-piston effect fixed ball valve products as standard products, and double-piston effect products as optional products. |
DIB | 1. Suitable for high temperature, low temperature, flammable, explosive, toxic, corrosive and other dangerous medium piping systems; 2. Suitable for occasions where frequent maintenance is required and the personal safety of maintenance personnel needs to be ensured; 3. Suitable for the conditions of fluid meter calibration systems. For example, in the case of flowmeter calibration, it is necessary to ensure that the medium retained in the system valve cavity will not leak into the test pipeline to affect the measurement accuracy. Once there is a slight leakage of the valve, it will cause measurement errors; 4. Suitable for applications where the tolerance for leakage is very low and the requirements for downstream sealing are very high. | A relief safety valve must be installed for the valve with two double-piston seats. |
Conclusion
Although DBB and DIB ball valves have been widely used in oil and gas long-distance pipeline projects, some users, designers, manufacturers and supervision personnel still lack a correct understanding of the principles and functions of these two types of valves.
Through detailed discussion and analysis, we believe that the two types of trunnion ball valves are different in structure, fluid barrier performance, sealing performance, applications, etc. And trunnion ball valves sometimes do have installation direction requirements. This article aims to improve people’s understanding of DBB and DIB trunnion ball valves, and ensure that the selection and design of the valves meet the requirements of the standard specifications. Provide a reference for engineering designers, valve manufacturers, and on-site construction personnel about the sealing structure and direction of the fixed ball valve through this blog’s analysis and conclusions.
Resource: This blog is translated from the article <Sealing Structure and Directional Analysis of DBB and DIB Type Fixed Ball Valves> published on Chemical Equipment and Pipeline, Volume 53, Issue 5 by Wu Jun. Article ID: 1009-3281 (2016) 05-0077-006.